Four Airflow Problems You Can Easily Discover with Static Pressure Testing
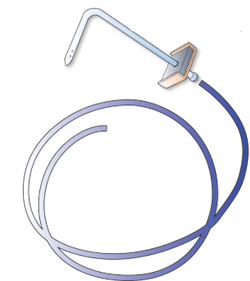
There are still many in our industry who don’t understand static pressure measurement as a troubleshooting skill. Instead, they see it as smoke and mirrors or hocus pocus, and more work on each call. The readings have no value to them.
This approach is a mistake. The truth is that static pressure testing makes you a better technician or salesperson, exposes the problems behind many customer complaints, and uncovers additional opportunities to serve them better. Many of these issues relate to airflow, and static pressure makes that connection.
If you’re tired of dealing with ongoing equipment problems, costly callbacks, and unhappy customers, there is a better way.
Let’s look at four airflow issues you can discover and solve with static pressure testing.
1. Low Fan Airflow
A wise man once taught me that “air” is the first word in air conditioning. When it is incorrect, nearly every other function of the system suffers. Airflow makes or breaks a system – just ask any technician who has struggled to diagnose a unit that intermittently freezes up or trips a safety switch.
The installation instructions for most air-handling equipment include a fan performance table. These tables provide a quick and easy way to estimate how much air the blower is moving. The tables are specific to the equipment model number, so find this table first. A quick Google search often yields excellent results if you can’t find it in the instructions.
To use the fan table, document the operating fan speed and then measure total external static pressure (TESP). Find these two points on the fan table and intersect them to plot fan airflow. It’s important to note that the blower must be clean for the tables to be accurate. If the blower is dirty, clean it first, and then proceed with testing.
Implementing this one static pressure test starts you in the right direction. You won’t have to guess anymore. Before you attach refrigeration gauges to the service valves on your next call, consider using this test first. As you advance in your career, you can add direct airflow measurement with instruments like a Digital TrueFlow Grid from The Energy Conservatory (TEC).
2. Dirty or Restrictive Indoor Coil
A common airflow restriction many technicians check is the indoor coil. But it takes a lot of time to disassemble cabinets and visually inspect the coil. And even then, you still can’t see past the surface. You can get the same results with two pressure measurements and a quick calculation – no disassembly required.
To measure coil pressure drop, take a static pressure reading entering the coil and one leaving the coil. Then, to calculate the coil pressure drop, subtract the leaving coil pressure from the entering coil pressure.
Ideally, a clean indoor coil’s pressure drop should range between .20-in. to .30 in. w.c. (inches of water column). The coil is probably clean if the pressure drop is within this range. But if the pressure drop is exceptionally high, you know the coil is likely dirty, restricted, or damaged and needs further investigation.
Be aware some newer indoor coil designs are very restrictive to airflow. They could have pressure drops exceeding .30-in. and be perfectly clean. A less restrictive coil would be a better choice in this situation.
3. Restrictive or Dirty Air Filter
Measuring filter pressure drop allows you to determine if your filter is either too restrictive or dirty. A restrictive air filter can degrade system airflow by 40% or more. A dirty filter is easy to discover, but what about the MERV 5000 air filter that chokes airflow but is clean?
You measure filter pressure drop by taking a static pressure reading entering the filter and one leaving the filter. Subtract the leaving filter pressure from the entering filter pressure. Ideally, filter pressure drop should not exceed 20% of the fan’s maximum rated external static pressure. With the average fan in a residential system rated for a maximum TESP of .50-in., filter pressure drop should not exceed .10-in. (20% x .50 = .10).
You measure filter pressure drop by taking a static pressure reading entering the filter and one leaving the filter. Subtract the leaving filter pressure from the entering filter pressure.
If filter pressure drop exceeds .10-in., you’ll need to upgrade parts of the duct system for it to work correctly. You can use a filter media with a lower pressure drop or add more filter surface area by increasing the filter size.
4. Duct System Restrictions
Undersized ducts are an epidemic in our industry. Single pressure readings taken near the equipment in the supply and return duct system can help you find restrictions or tell you if the duct is undersized.
Pressure readings before the air filter provide return duct pressure. Pressure readings after the coil provide supply duct pressure. Look for measured pressures that are less than .10-in. If duct pressures exceed this value, there is a good chance that side of the duct system has a restriction.
Measure duct system pressures every four feet along the system to identify further restrictions.
Measure duct system pressures every four feet along the system to identify further restrictions. When you see a drastic change in duct pressure, you’ve likely found the restriction. Loose duct liners, closed fire dampers, and collapsed ducts are common restrictions.
Don’t Procrastinate
There’s no time like now to start. If you’re serious about measuring static pressure, contact me and I’ll start you on the right path with some free static pressure testing procedures. Going into the spring maintenance season is the best time to begin.
You’ll also need the following test instruments and accessories to measure static pressure. Some of these items may already be in your tool bag. A good static pressure test kit consists of the following:
- digital manometer or micromanometer
- one length of tubing
- one static pressure tip
- 3/8-in. bullet tip drill bit with a sheath to prevent drilling in too far
- supply of 3/8-in. plastic test port plugs
- carrying case.
Make sure you’re equipped with the right stuff. Otherwise, you’ll get frustrated and stop short of success. The best place to start testing is on your own HVAC system or one in the office. Doing this allows you to build confidence before going live with customers.
As your skills progress, you’ll see your troubleshooting abilities grow rapidly. Please send me your favorite airside defects and how you discovered them using static pressure testing. I would love to share the results and your stories behind them.
David Richardson serves the HVAC industry as Director of Training for the National Comfort Institute, Inc. (NCI). NCI specializes in training that focuses on improving, measuring, and verifying HVAC and Building Performance.
If you’re an HVAC contractor or technician interested in learning more about static pressure testing, contact David at ncilink.com/ContactMe or call 800-633-7058. NCI’s website, www.nationalcomfortinstitute.com, is full of free technical articles and downloads to help you improve your professionalism and strengthen your company.
About the Author
David Richardson
Director, technical curriculum
David Richardson serves the HVAC industry as director of technical curriculum at National Comfort Institute, Inc. (NCI), Avon, Ohio. NCI specializes in training that focuses on improving, measuring, and verifying HVAC and Building Performance.